Nowadays, load carrier tracking or load carrier monitoring can be used to significantly optimize a company's flow of goods, which not only increases the transparency of transport processes but also improves the efficiency of supply chains. In many companies, the management of load carriers is not yet automated or not automated enough.
Typical load carriers such as:
- Steel tank
- Box pallets
- Pallet and pallet frame
- Stacking and transport racks
- Small, large and special load carriers
often cause long turnaround times in plants or poor utilization due to shortages or overstocks, resulting in search times that lead to downtime and additional costs for additional load carriers. Inefficient processes due to a lack of knowledge about the condition or whereabouts of the load carriers are often the result. But this does not have to be the case: Those who use modern load carrier tracking can not only better control logistics processes, but also optimize them.
With a modern load carrier tracking system, it is the combination of modern technology (hardware) and intelligent software that gives today's companies significant advantages. This includes, for example, detailed information at any time about:
- Travel times
- Standing times
- Loading times
- Compliance with approved geographical zones (theft control)
- Checking whether load carriers have been loaded onto the correct vehicle
- Control, over the whereabouts of the load carriers
- Delivery control of the load carriers (Have they already been delivered to the destination?)
- Vehicles still on schedule
Those who monitor their load carriers in this way avoid uncertainty, unnecessary delays and do not have to pick up the phone to make endless search and check calls.
Why is optimized supply chain management important?
Those who optimize their supply chain management - and load carrier tracking is an important tool for this - can reduce the costs of the logistics chain and thus help to keep production flexible and in line with demand as well as to optimize costs throughout. To ensure that problems in the value chain have as little impact as possible on the end customer, perfect control of the flow of goods and information along the entire supply chain is required.
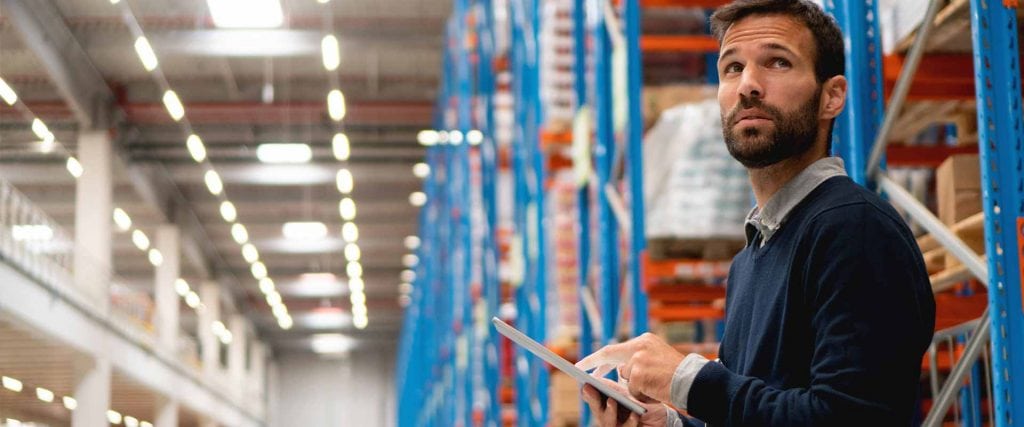
What can be achieved through optimal supply chain management?
Optimal supply chain management not only tracks information on how a product is created and gets to the end customer's shelf, but also returns information such as:
- Customer feedback on specific goods or deliveries
- Problems in distribution
- Wishes of the production to suppliers
Companies that successfully manage supply chains often achieve the following goals:
- Cost reduction
- Acceleration of deliveries up to same-day delivery
- Enabling innovation
- Efficiency improvement
- Optimization of the information flow
- Better management of cash flows
- Improve relationships with customers and suppliers
Prerequisite for good supply chain management:
Only when all links in the value chain work together optimally does comprehensive knowledge of the common processes emerge. Load carrier tracking is an essential building block for this. This means that you no longer have to rely on guesses or assumptions as to why certain processes do not work, but can monitor and check the processes in detail.
To improve supply chains, constant communication between the partners involved is important. Only those who exchange information about strengths and weaknesses can optimize suboptimal aspects.
Speed along supply chains also requires responsibilities: In supply chain management, responsibilities and expectations must be clearly defined. Binding agreements and specifications as well as their control lead to success.
Only those who know where the parts required for the production process are located at all times can guarantee a smooth and automated material supply for production. With optimized load carrier tracking, every container with raw materials or semi-finished products that are required for further processing can be tracked precisely so that production and delivery delays can be significantly minimized.
Delivery promises to customers can be met through load carrier tracking
Those who have created real-time visibility through load carrier tracking can not only reduce buffer inventories and save on personnel searching for containers, loads or supplies, but also help keep delivery promises to customers.
What is meant by charge carrier tracking?
Logistics in production and distribution cannot do without the typical load carriers. Knowing at all times what condition these load carriers are in and where they are provides significant advantages over competitors who do not know this. This applies to all types of load carriers.
The most common load carriers in German-speaking countries are:
- Euro pallets (European standard EN13698-1)
- Large and small load carriers (GLT/KLT)
- Half and quarter pallets, e.g. also Düsseldorf pallet
- Chemical pallets (CP)
- Lattice boxes with steel frame lattice structures
- Big bag for transport and storage of bulk material
- Intermediate Bulk Container (IBC), e.g. for paints or free-flowing material
- IFCO boxes for fruit and vegetables
By integrating additional technology into the load carrier, the load carrier also becomes an information carrier and makes load carrier tracking possible in the first place.
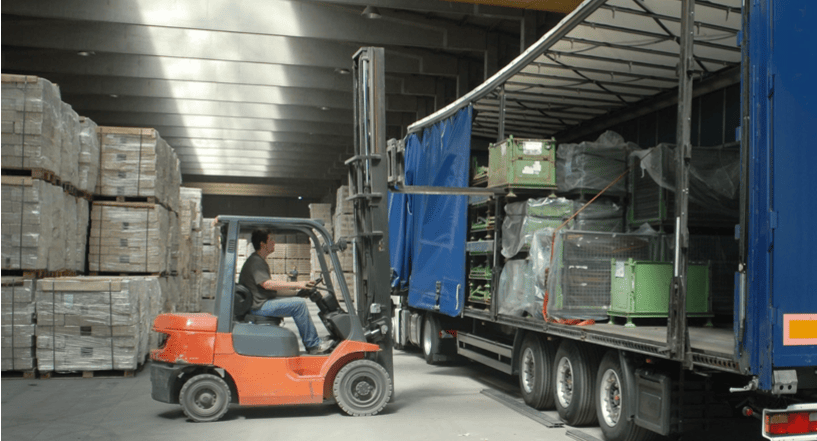
The load carrier tracking enables:
- Overview of the load carrier inventory at all times
- Seamless monitoring of changes in the location and status of load carriers and loads
- Improvement of the load carrier utilization
- Reduction of load carrier wastage
- Localization of load carriers
- Coordination of maintenance intervals
However, it is not only the integration of the hardware into the load carriers that is crucial, but above all the intelligent networking through software. Software solutions such as thingsHub provide entrepreneurs with a platform on which they have a full overview of goods flows, deliveries and inventories, and thus smooth production and warehouse control.
What technology is used for load carrier tracking?
Load carrier tracking is done by networking information provided mainly by the following technology:
- RFID
- RTLS
- GPS
- BLE
- UWB
- WLAN
These technologies have the advantage that the manual scanning of barcodes can be dispensed with in many places, as incoming and outgoing goods or storage can be automatically recorded in the system. Parcels can be loaded onto pallets by type without manual scanning and processes can be triggered automatically.
Which tracking technology is the best?
There is no such thing as the best tracking technology or the best tracking module. Each system has its right to exist in certain areas and depending on the use case requirements. While RFID systems enable very precise tracking, but only have a short range and high installation costs, GPS can track load carriers over a long range worldwide without requiring large infrastructure. Which system offers the best function in which business area and which systems should be combined, if necessary, should be worked out together with experts in order to avoid bad investments.
What are the biggest advantages of load carrier tracking?
In companies that are already successfully tracking their load carriers, the following four key benefits are repeatedly cited:
- Increased efficiency in tracking and controlling loads and flows of goods
- Optimization of inventory and warehouse management
- Cost reductions through better planning and resource allocations
- Increase customer satisfaction and service improvement
Where can particularly high savings be achieved through professional load carrier tracking?
In many companies, double-digit percentage improvements can be achieved in the following areas:
- Due to a higher utilization of the load carriers, less new investments are necessary in this area
- Shrinkage of load carriers is significantly reduced
- Reduction of search, inventory and scanning effort
- Saving coordination effort and obtaining status updates
What does a company have to do to reap the benefits?
The introduction of professional load carrier tracking is a complex project in which the specialists at SmartMakers are happy to support companies of all sizes with their experience. As a rule, the process is divided into three phases:
I. Capture what load carriers and load flows are present in the company and where an improvement of the data flow could bring significant benefits.
II. selection and installation of the required hardware.
III. Installation and instruction of the software, networking with the company's own systems.
The decisive criterion for deriving the greatest possible benefit from such systems is not a special RFID chip or a low-cost GPS module, but rather only the know-how gained from many installations leads to a perfect symbiosis of hardware, software and existing information technology in the company. If a system is perfectly planned and implemented, cost and competitive advantages for the company result, which make the costs for the introduction and operation of such technologies fade into the background.
Would you like to delve even deeper and find out how intelligent fleet management for load carriers can be realized with IoT ? Read more here.
Conclusion:
Today, successful companies rely on professional load carrier tracking with state-of-the-art technology, which helps to reduce costs and optimize processes by obtaining additional information. Today, not operating load carrier tracking professionally, or not at all, means a significant disadvantage compared to the competition. If you want to achieve a high level of customer satisfaction at competitive prices, you should be able to track the flow of goods from suppliers to customers within your own company and thus have all the information needed to make business decisions. Optimized container logistics can already be mapped today with real-time tracking for load carriers. This includes everything from small load carriers (KLS) to euro pallets and large load carriers. If you know where your pallets or containers are at any given time and what they are carrying, you can use real-time analyses to gain such great advantages that competitors who cannot do this lose out.
In principle, the technology required for this is very cost-effective in relation to the benefits. The tracking of load carriers is becoming increasingly important, especially in light of the shortage of skilled workers and the discussion about the climate crisis: the automatic flow of information can save personnel who would otherwise be occupied with search or coordination tasks. Optimization also means that fewer journeys are required, which saves tons of CO2.