The world of maintenance is being revolutionized by the Internet of Things (IoT), enabling predictive maintenance techniques that help organizations optimize equipment uptime, prevent breakdowns and minimize operating costs. In this article, we will explore the world of predictive maintenance at IoT , its definition, benefits and how it works.
What is predictive maintenance?
Predictive maintenance is a proactive maintenance strategy that uses data analytics and machine learning algorithms to predict equipment failures or malfunctions before they occur.
This approach enables companies to schedule maintenance at an appropriate time to avoid equipment failures and minimize downtime. Predictive maintenance is essential for industrial operations, helping companies avoid costly repairs and equipment replacements and improve safety and reliability.
The role of IoT in predictive maintenance
The role of IoT in predictive maintenance is crucial. IoT Sensors embedded in machinery and equipment collect real-time data on equipment performance, which is transmitted to a central data storage system for analysis.
According to McKinsey & Company research, IoT-enabled predictive maintenance can cut maintenance costs by up to 30%, reduce downtime by up to 45% and extend equipment life by up to 20%.
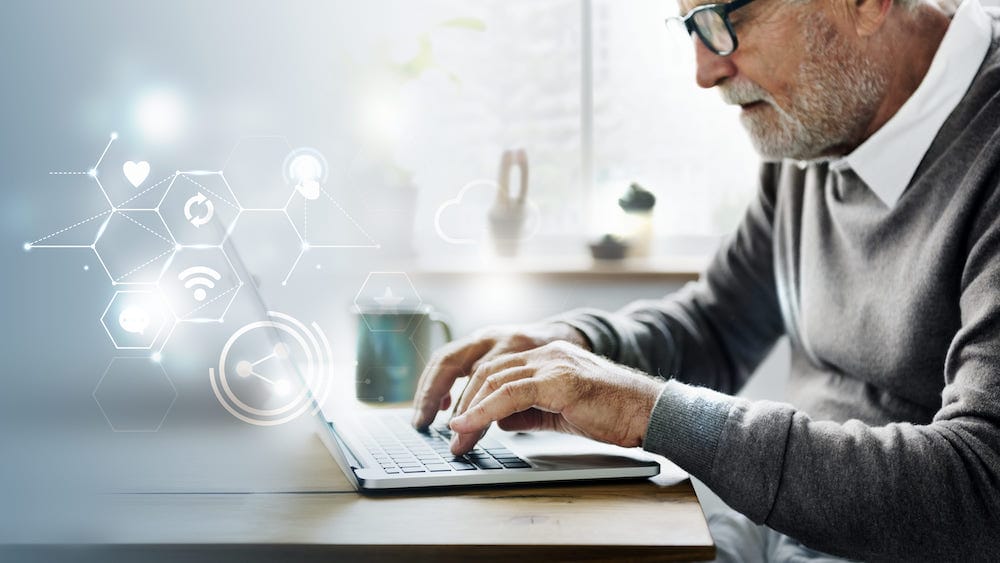
By harnessing the power of machine learning and artificial intelligence algorithms, IoT predictive maintenance systems can recognize patterns, identify anomalies and generate alerts that enable companies to take corrective action before a major equipment failure occurs.
IoT-based predictive maintenance architecture
To perform predictive maintenance based on IoT , organizations need a system that includes several key components. These components work together to collect, store and analyze device performance data to predict and prevent device failures.
IoT Sensors
First, for predictive maintenance based on IoT , sensors are embedded in machines and devices to collect real-time data on device performance. These sensors are designed to detect changes in temperature, pressure, vibration and other critical parameters that indicate the condition of the equipment.
Data communication
Second, data communication is critical for transmitting real-time data from sensors to a central data storage system. Communication can be via wired or wireless networks and data transfer protocols such as MQTT, CoAP or HTTP. A robust data communications infrastructure ensures that data is transmitted securely and reliably and provides organizations with real-time data on device performance.
Centralized data storage
Centralized data storage is critical to store and manage large amounts of data collected by IoT sensors. Cloud-based storage solutions such as AWS, Azure and Google Cloud provide scalable and secure storage for IoT data. The centralized storage system provides a single source of truth for device performance data, enabling organizations to identify trends, patterns and anomalies that could indicate potential failures.
Predictive maintenance software
Predictive maintenance software is used to analyze the data collected by IoT sensors to detect patterns, identify anomalies and generate alerts. Predictive maintenance software uses machine learning and artificial intelligence algorithms to learn the behavior of devices and identify potential faults. The software can also generate predictions about when maintenance work is required, allowing companies to proactively plan maintenance schedules.
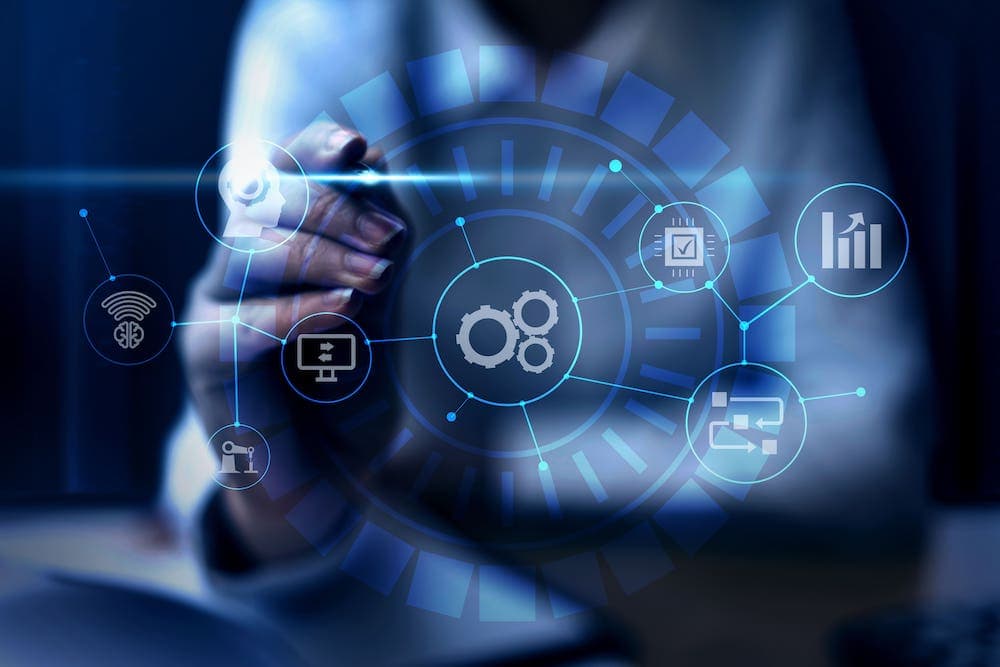
Analytics
Finally, analytics tools are used to visualize and interpret data collected from IoT sensors. These tools give organizations insights into equipment health and performance, patterns and trends, and root causes of problems, so they can make informed decisions about maintenance and repair schedules and reduce costs.
Main advantages of predictive IoT maintenance for companies
First, it enables companies to identify and resolve equipment issues before they escalate to major problems, reducing the frequency of unexpected equipment failures and minimizing downtime. This improves equipment uptime, resulting in increased productivity and revenue.
Second, predictive maintenance helps companies optimize maintenance schedules, resulting in cost savings through reduced maintenance and repair costs.
Third, predictive maintenance improves workplace safety and reduces the risk of equipment failure, which reduces the likelihood of accidents. This can prevent injuries and fatalities in the workplace.
Fourthly, predictive maintenance with IoT improves the service life of systems, extends the service life of devices and reduces the frequency of replacement and upgrade requirements.
Use cases for predictive IoT maintenance
IoT-based predictive maintenance is being used successfully in various industries, including manufacturing, transportation and energy.
Manufacturing
In the manufacturing industry, predictive maintenance with IoT solutions can help identify potential equipment failures before they occur to reduce downtime and improve productivity. For example, a heavy equipment manufacturer can use sensors to monitor equipment performance and detect changes in vibration patterns that could indicate potential equipment failure. Predictive maintenance software can analyze this data and generate alerts when maintenance is required, allowing the manufacturer to proactively schedule repairs.
Oil and gas
In the oil and gas industry, predictive maintenance using IoT can help to avoid unforeseen downtime and reduce maintenance costs. Sensors can be installed on equipment such as pumps, compressors and turbines to monitor equipment performance in real time. This data can be analyzed using predictive maintenance software to identify potential equipment failures and generate alerts when maintenance is required. This proactive approach to maintenance can help avoid costly unforeseen downtime and reduce maintenance costs.
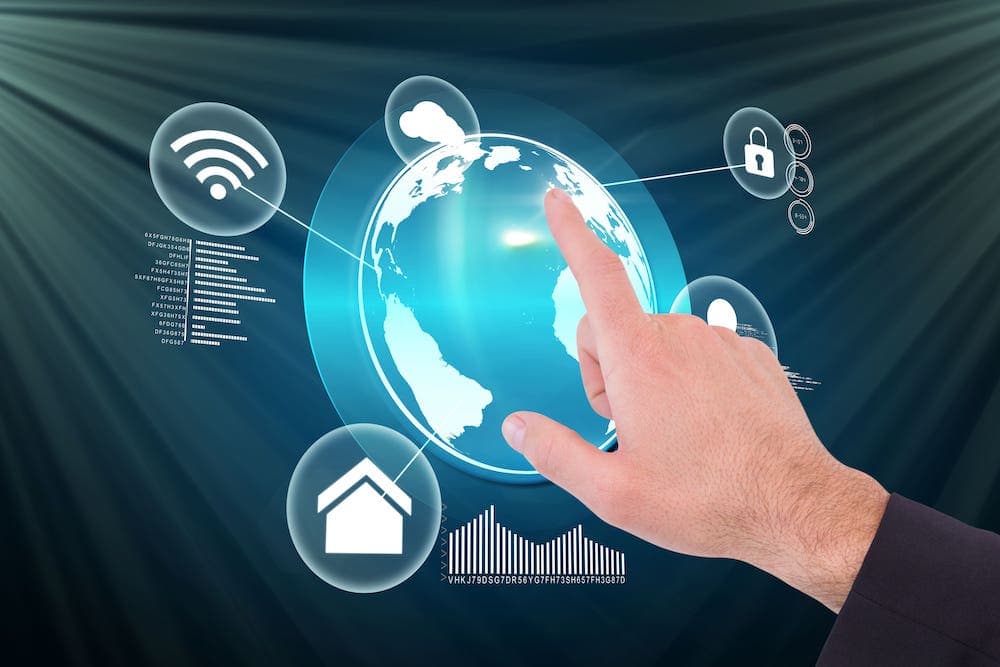
Transportation
In transportation, predictive maintenance using IoT sensors can help improve fleet reliability and reduce maintenance costs. IoT-Sensors can be installed on vehicles to monitor engine performance, tire pressure and other key parameters. This data can be analyzed using predictive maintenance software to detect potential equipment failures and generate alerts when maintenance is required. This proactive approach to maintenance can help transport companies minimize unforeseen downtime and reduce maintenance costs.
For example, global manufacturing company Siemens uses industrial IoT predictive maintenance to monitor and maintain wind turbines. This allows them to predict potential failures and optimize maintenance schedules.
Another example is the US logistics company UPS, which uses IoT sensors to monitor the condition of its delivery vans in order to reduce maintenance costs and increase vehicle availability.
Final thoughts
IoT Predictive maintenance is fast becoming a game changer in the maintenance industry. By using IoT devices, predictive analytics and machine learning algorithms, organizations can predict potential equipment failures, reduce downtime and optimize maintenance schedules.
Although IoT predictive maintenance comes with its own challenges and risks, the benefits far outweigh the disadvantages. With proper planning and execution, organizations can successfully implement IoT predictive maintenance and stay ahead of the competition.